Free Shipping Sitewide | 1 Year Warranty
Optimizing Warehouse Operations with Picking Equipment
Streamline warehouse operations with picking equipment—boost accuracy, speed, and efficiency for order fulfillment and inventory management.
4/29/20258 min read
Optimizing Warehouse Operations with Picking Equipment
In the hyper-competitive realm of logistics and supply chain management, the efficiency of warehouse operations is of great concern.
Order picking, which involves the retrieval of inventory items to be included in customer orders, is the crux of the matter as far as efficiency is concerned.
Warehousing equipment meant for picking tasks are instrumental in expediting this task, thereby bringing about higher efficiency and less error.
The rise of e-commerce businesses and the quickly escalating consumer demands have created a need for new and effective picking solutions that is more demanding than never before.
This article, therefore, is centered around the available types of picking equipment, their virtues, and also the paradigms to be followed for implementing the same in warehouse operations.
On the one hand, progress in warehouse picking devices has largely been due to technological advancement; and on the other, it was the quest for streamlined operations that moved the process forward.
Technology has changed it all. You can hardly recognize any of the old manual machines as the change in the face of the tools and the systems of the whole process has been more than ever. The ball is now in the warehouse managers' court.
They should know the types of picking equipment together with their specific applications, which in turn will enable them to walk informally but confidently into the realization of their operational objectives.
The feature of warehouse picking equipment presented herein is crystal clear in showing the importance of the tools that are the perfect fit for supporting the entire fulfillment process in a consistent manner.
Key Takeaways
Warehouse picking equipment includes tools and technology used to pick and fulfill customer orders in a warehouse setting.
Warehousing pieces of equipment that fall under picking are usually pick carts, pick-to-light systems, voice picker systems and automated guided vehicles (AGVs).
The advantages of incorporating picking equipment in warehouse operations are increased efficiency, accuracy, productivity as well as reduced labor costs and order fulfillment times.
The factors to think about when choosing picking equipment are the layout of the warehouse, the volume of orders, the diversity of SKUs, and the constraints on the budget.
Adherence to the industry's best practices in terms of picking equipment’s implementation in warehouse operations encompasses various aspects such as an accurate needs check, ongoing training for employees along with frequent assessments and performance optimization.
Types of Picking Equipment
Warehousing technology can be distinguished by whether it is manual or automatic, with the former following human direction and the latter being computer-controlled.
For example, a warehouse worker can have a hand truck when moving heavy boxes or pallets over short distances in a warehouse, and a picker could employ a picking cart while picking several items at one time to reduce the number of journeys needed
AGVs are the ones that are mainly responsible to navigate through the warehousing and that too autonomously. They are the ones that have a role of getting goods from one place to another without any operational assistance by a human.
With the help of advanced robot picking systems, goods can be taken out from the shelves by itself using the algorithms and machine learning, which indeed reduce labor costs and errors by humans to the bare minimum.
Deciding between manual and automated equipment choices is mostly influenced by warehouse size, the number of orders, and how much money is left in the bank.
Benefits of Using Picking Equipment in Warehouse Operations
Selection of the right picking equipment can bring a lot of benefits to the warehouse operations. The primary one is the saving of time, and, therefore, the direct one is an increase in efficiency.
With the help of high-performance pieces of equipment that are also utilized only for specific tasks, the operation is such that it can hardly be believed to be faster than before, so, the time required for order fulfillment is reduced as if on demand.
For example, through the use of a picking cart, staff members not only take the items in a larger number, but also are able to make fewer trips in gathering than the latter which is only time-consuming.
Implementing the picking equipment not only saves time by not exposing staff to prolonged picking activities but also reduces labor costs. Picking equipment also helps to reduce order fulfillment errors in addition to efficiency improvement.
Usually, the process of manual picking is prone to mistakes. Mis-picking and over-picking are typical examples that result from manual picking.
Differently, when accompanied by automated systems with the latest technology of barcode scanning, the warehouse is surely guaranteed to reap the cream.
To explain, by the use of barcode scanners in automation systems, the correct packing and picking of items are assured, hence, the mistakes are minimized, and the order will have accurate packing.
This reduction in errors not only gets the customer more satisfied but also decreases the amount of expensive returns and re-shipments.
Factors to Consider When Selecting Picking Equipment
Factor description ergonomics the equipment should be designed in such a way as to reduce the operator’s risk of injury during the picking process.
Through put the equipment should make sure that the items are picked at the required rate that the warehouse manager desires.
Accuracy most of the time, the equipment should be able to select the products accurately to reduce the number of errors it commits.
Flexibility the equipment should not be difficult to adjust to different products and should also adapt well to new picking processes.
Space utilization the equipment should not only be space-saving but also should help with the flow of goods throughout the warehouse.
Cost the equipment should be a good investment that will bring in money and at the same time it should be in compliance with the budget restrictions.
When selecting picking equipment for a warehouse, there are several main issues the company needs to consider so that efficiency and return on investment can be guaranteed.
The first that comes to mind is the products that are stored. Productivity may be increased through this, however, it is important that it be safe and healthy.
Different products might need to be handled in different ways; for instance, delicate items may require special equipment that brings in minimal moving during transportation.
Furthermore, the size and the weight of products may influence what equipment would be the best fit; the heavier the items, the more likely the powered lifting devices should be used, while manual tools may even suffice for the smaller ones.
Also, the warehouse itself has to be taken into account as one of the most important considerations. The space where the warehouse is located, in other words, the configuration of the aisles, the shelving units, and the storage areas may have an effect on the productivity of some picking equipment.
An example of this is that the narrow aisles may not be the right place for the large automated vehicles, but they could very well be the proper place to use the small manual carts.
In addition, being aware of the number of daily orders that are being processed is a must; the high-volume companies may not think twice about acquiring a set of automated systems that can work with mass quantities, even swiftly, whereas the small-scale ones would be better off using manual solutions more economically.
Picking Equipment Best Practices for Warehouse Operations Implementation
The implementation of picking equipment requires a primarily focused planning process, compliance to the implemented practices that will ensure one will get the highest benefits and productivity of the equipment.
Among the good practices are the pre-evaluation of the current processes before the installation of the equipment.
Through the observation of the areas that require changes, the managers can go ahead and select the equipment that will exclusively handle these issues.
Furthermore, creating links between current warehouse management systems and the delivery of the goods can always be a plus to the pick system.
For example, placing mobile devices on the manual carts that synchronize with the WMS gives the possibility to receive the status of the order and the stock levels even when they are to go around.
This also enables efficient communication, as well as allowing the management to control the productivity of the employees and make decisions based on the facts about the staffing procedure during the whole process.
Training and Safety Protocols for Using Picking Equipment
The implementation of picking equipment successfully relies on training that is wholehearted, so the employees should be trained well with the latest tools and in a way that they know that they are safe and effective.
Training is supposed to cover not only the use of equipment but also the most suitable ways of carrying out safety procedures in the warehouse.
For example, workers should be made aware of the proper lifting methods to be applied when handling manual tools so that they may avoid injuries experienced when lifting heavy articles.
Moreover, there is a need to draw up safety protocols in order to reduce the risks of dealing with automatic systems.
One way of doing this is by carrying out regular checks to decide whether the equipment has the right functions and is safe for use or not.
Additionally, the making of clear instructions on emergency procedures that should be followed in case of equipment breakdown or accidents is a vitally important aspect of keeping a working environment safe.
Warehouses that put the emphasis on training and safety protocols are able to create a safety conscious environment while also raising the productivity levels of their picking operations.
Case Studies: Successful Implementation of Picking Equipment in Warehouse Operations
Studying actual cases of successful implementation of the picking equipment in warehouse operations can offer practical insights into how to maximize the use of picking equipment in the warehouse.
For example, one prominent instance is that of Amazon, which has completed the renovation of its order filling procedures through the application of the most advanced of the automation systems.
The company, by using a blend of automated robots and human workers, manages to pick the orders most effectively.
Robots can carry shelves stocked with goods directly to workers, thereby significantly minimising transit time and likewise, boosting the overall efficiency.
The introduction of this kind of equipment is of great use to Walmart which makes great emphasis on automated pallet jacks at its distribution centres.
Its adoption has not only facilitated the stock management procedures, but it has brought down the expenses associated with the workforce in the company.
The company made this one-time investment and the consequent benefits ensued in the form of the reduction in errors in the orders as well as an increase in performance speed of the same.
These cases are a demonstration of how one can bring about a huge change in the functionality of a business and place it in a position to outcompete in the market with the help of the right choice of the picking equipment.
Future Trends in Warehouse Picking Equipment
Due to the rapid pace of technological advancements, the warehouse picking equipment industry is on the brink of a major makeover.
One of the main developing trends is the higher acceptance of artificial intelligence (AI) and machine learning algorithms in robotised systems.
These are able to bring new levels of automation to robotic systems so that they can self-sufficiently adapt to sudden changes in the store and dynamically refine their selection paths.
Moreover, augmented reality (AR) technological advances are seen as the next step in enhancing a manual picking process.
AR-based solutions are going to give a real-time visual demonstration to the workers and thus the process of finding items in storage will become faster and more accurate during order fulfillment.
With the development of these technologies and their affordability, warehouses could move towards more hybrid options where both manual and automated systems are combined in order to reach the highest levels of efficiency.
Altogether, every business enterprise that needs to guarantee a growth in operational efficiency, meet the increasing consumer demands, and -- at the same time -- save on costs, the warehouse picking equipment is their go-to solution.
Through being conversant with the types of equipment, their advantages, ways of introducing and training, and what might come next, establishments can assure of their leading position in the market full of tough competition.
Leading provider of heavy equipment solutions in the US such as mini excavator diggers and skid steers. When looking for a reliable mini excavator supplier, look for New Excavator. Quality compact mini excavators backed by a strong after sales service and a widespread inventory of spares.
Contact us for equipment inquiries
© 2025. All rights reserved USA EXCAVATORS
Follow us now
Our location
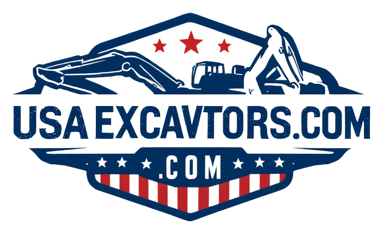
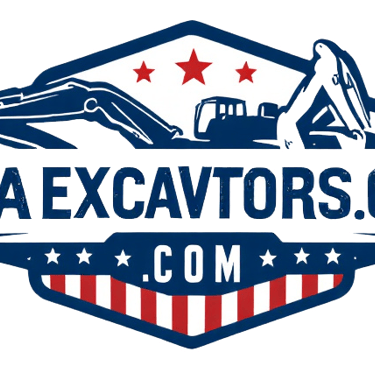